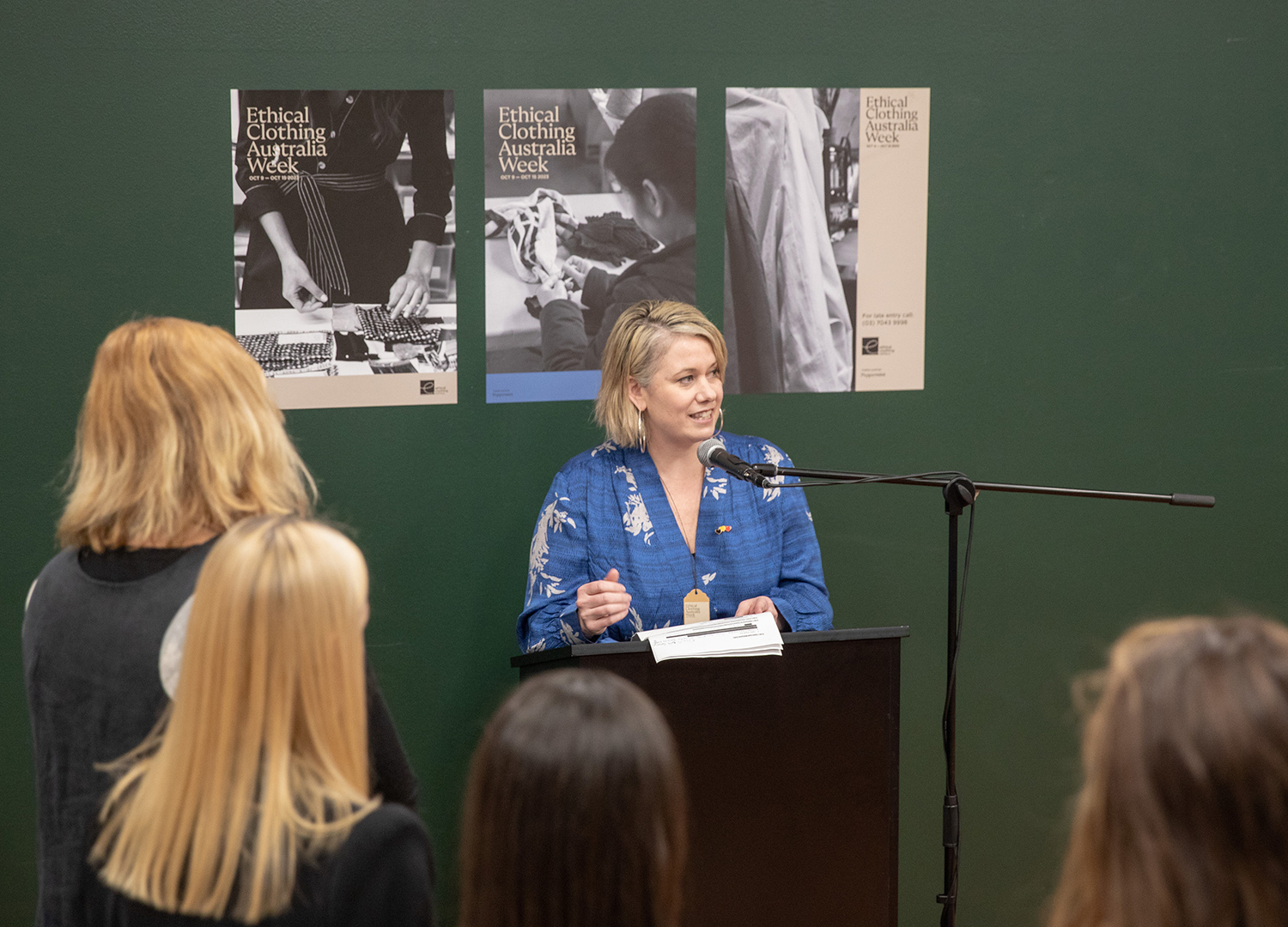
People, Place and Process: The Future Looks Bright for Fashion Down Under
words CAITLIN MORIARTY above RACHEL REILLY, NATIONAL MANAGER OF ETHICAL CLOTHING AUSTRALIA, PHOTO BY DAN CAHILL
“Let’s work together to make an extraordinary industry stronger.” These words from Rachel Reilly, the national manager of Ethical Clothing Australia, marked the launch of ECA Week 2023 – a week-long series of in-person events across Melbourne and Sydney to recognise businesses who have committed to ethical manufacturing in the textiles, clothing and footwear (TCF) industry in Australia.
Sustainable and ethical fashion is a part of our DNA here at Peppermint. Our team was extremely proud to be on the ground in Melbourne – visiting everywhere from factories and showrooms to shopfronts and offices to learn more about the work, knowledge and passion that goes into protecting the rights of the 477,000 workers – 77% of whom are female – that are part of the Australian TCF industry alone. Here are the three ideas we’ll be ruminating on long after the week that was.
above LAUNCH OF ECA WEEK 2023 AT COLLARTS IN FITZROY, PHOTO BY DAN CAHILL
Accountability and transparency are everything
“To get ECA accreditation, businesses must go through what is considered one of the most rigorous and robust audits globally,” Rachel says. The ECA audit sees every part of the business, from design to dispatch, assessed – with keen interest across fair pay and safe working conditions for every person across the supply chain including homeworkers (formerly known as outworkers). “These are often women who are in isolated situations and can be quite invisible down that supply chain,” says Rachel. “As you can imagine, they can be quite prone to exploitation.”
To get ECA accreditation, businesses must go through what is considered one of the most rigorous and robust audits globally
To ensure consistency for workers and consumers, businesses that sign up for ECA accreditation also commit to the same audit – conducted with the same rigour – every year. It’s something that brands under the ECA umbrella have come to appreciate.
top RACHEL REILLY FROM ECA AND HANH LE FROM DENIMSMITH bottom CHOLE KERR FROM NEXT STATE. PHOTOS COURTESY OF ETHICAL CLOTHING AUSTRALIA
Hanh Le, product manager at Denimsmith in Fitzroy, says that ECA accreditation and events like ECA week are essential to shine a light on people often forgotten along the supply chain. “It’s important for us to showcase and divulge who our makers are,” she says. “That audit process keeps us accountable.”
Chole Kerr and Geoff Spink – co-founders of Next State, a digital textile printer and manufacturer in Thornbury – agree that accreditation means not only transparency but is also there to help consumers cut through the greenwashing. “From the very base level to the high level, accreditation shows we are completely compliant,” says Chole. “That gives our customers confidence that we can validate the claims we make.”
People come first
Technology obviously plays a huge part in the garment industry – with benefits including faster production times and turnarounds, efficient management of material and less physical exertion for workers. But one thing was clear during ECA Week 2023: people will always play a part in garment manufacturing.
Knovus, a shopfront and workshop in Carlton with a focus on knit services, boasts an incredibly innovative approach to manufacturing. Their investment in the Shima Seiki Wholegarment Knitting Machine – the only one of its kind in Australia – allows the Knovus team to produce zero-waste products using 3D knit technology.
If I’m going to be so heavily focused on sustainability, then a part of that has to be people
But even with advanced technology at hand, Knovus founder, Patricia Chircop considers people the centre of her business. “If I’m going to be so heavily focused on sustainability, then a part of that has to be people,” she says. “We’re moving from a circular economy to a wellbeing economy [that’s] designed to serve both people and planet. To me, a wellbeing economy is more valuable. When you look at the astonishing statistics around slave labour and fashion being a part of that – the facts are heartbreaking. It is a no-brainer for me.”
top PATRICIA CHIRCOP FROM KNOVUS bottom WHOLE GARMENT KNITTING MACHINE AT KNOVUS, PHOTOS COURTESY OF ETHICAL CLOTHING AUSTRALIA
At Vince Clothing, a garment factory in Brunswick East that specialises in manufacturing denim, we’re given the unique opportunity to view the factory after hours and learn more about the process of making a pair of Denimsmith jeans. Machinery dominates the space and Hanh (who works as Administration at Vince Clothing) tells us that each machine is serviced daily. We see a lathe trace and cut fabric with pinpoint accuracy, ensuring that denim wastage is minimised. A dedicated machine embroiders back pockets in a matter of seconds using predetermined templates. But behind all of the automation, a person is still very much in control – in this case, it’s the director of Vince Clothing, Vinh Le. As he stands at the computer connected to the lathe, confirming sizing and cuts, Hanh says, “He’s going to double-check everything before he cuts because this is very expensive fabric… so, no pressure!” The skills, knowledge and experience of a garment worker can’t be downplayed during manufacturing. “Of course we need machinery, but people will always be a part of the process, checking and double checking,” Hanh enthuses.
People will always be a part of the process, checking and double checking
It’s an issue that the garment industry in Australia will have to reckon with soon, as a population of skilled workers reach retirement age. At Vince Clothing, they encourage students and young people to come in and learn from older workers – but it can be a challenge. “It’s really hard to get young people in,” says Hanh. “Everyone wants to be a designer but no one wants to learn the garment knowledge it takes to be a designer.”
top VINH LE OF VINCE CLOTHING, PHOTO COURTESY OF ETHICAL CLOTHING AUSTRALIA bottom left COURTNEY HOLM OF A.BCH
Locally made is here to stay
The events of the last few years have drastically changed the landscape of garment manufacturing in Australia for the better. Issues with international shipping and material availability meant that businesses who had previously moved manufacturing offshore looked to their own backyards again.
Over at Denimsmith, making local is a central pillar of the business values. “In the last three years, there’s been a huge increase in local manufacturing,” says Hanh of Vince Clothing. “We’ve had a lot of traction since 2020.”
“We make everything in Brunswick East. We like to tell everyone it’s a 15-minute drive from the manufacturer, we get it washed and then it just drives over here and we showcase it,” she continues. “We keep a very tight loop in terms of our supply chain.”
We like to tell everyone it’s a 15-minute drive from the manufacturer, we get it washed and then it just drives over here and we showcase it
Other ECA-accredited businesses also prioritise local manufacturing, with businesses like A.BCH combining their workroom and showroom in a space in West Melbourne where you can try on their range while also watching founder Courtney Holm sew each piece.
This increased interest in and demand for local production means that while the rag trade may not be as booming as it once was, the possibility for continued growth is tremendous.
At Knovus, Patricia works with a suite of digital programs that allow her to simulate stitch structures and moves, creating extremely realistic simulations of knitwear stitches and designs – a mohair jumper looks ‘fluffy’ on screen, stitches can be tested more accurately for how they will look on various parts of a garment. By doing so, she’s not only improving workflow and lessening waste, it’s empowering her to pitch local production to a variety of industries, including fashion, furniture and even medical products.
“We’re not actually knitting a stitch, but we’re digitising everything and being able to get a really good read of what something is going to look like before we do it,” she says. “This allows us to keep the raw materials in the highest value state for the longest amount of time.”
“We’re not a very big operation, but with this technology, I can still get out units of 200 and do good production. I think there is immense opportunity here.”