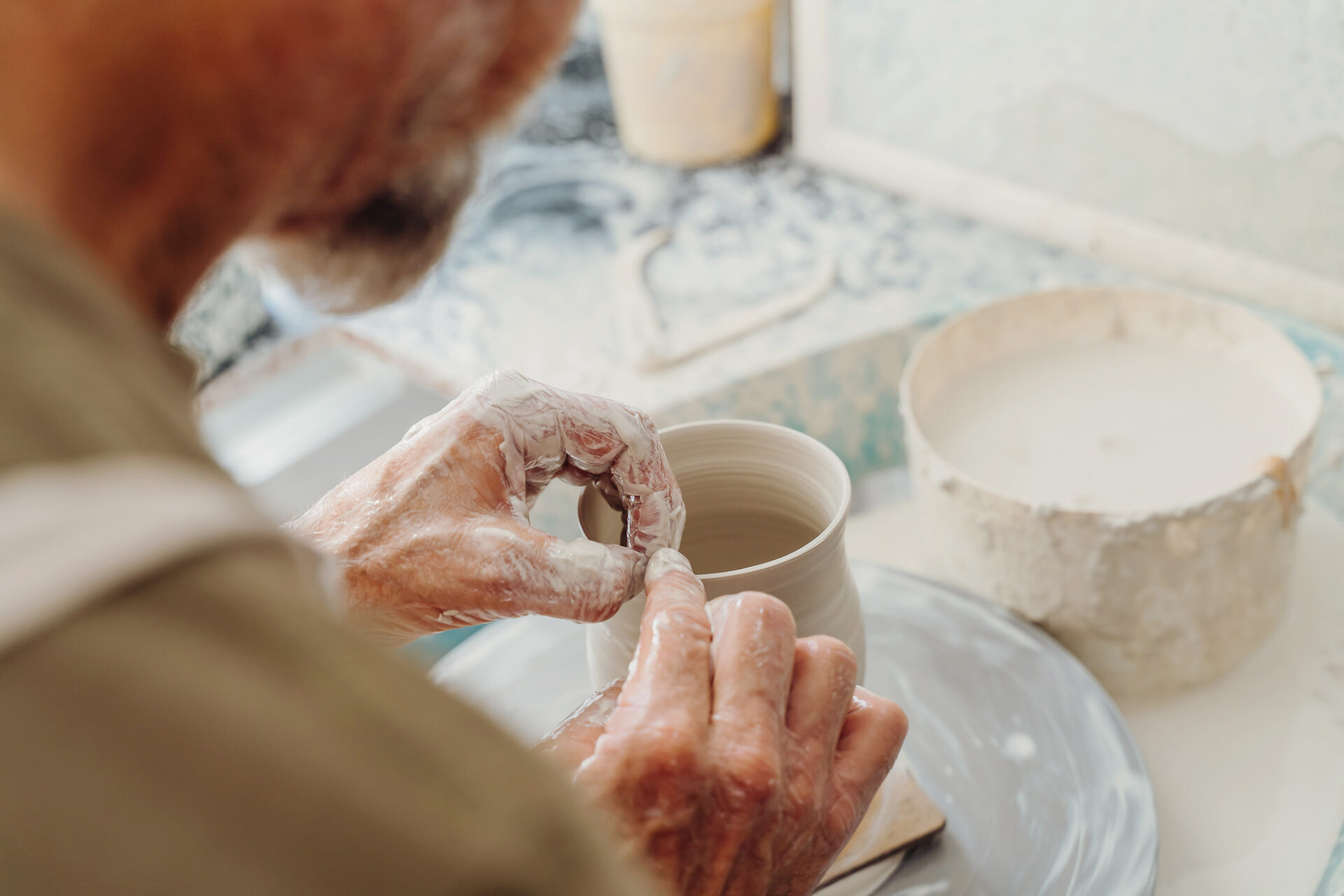
All Kilns Glazing: Meet the Local Pottery Brand Fighting for the Planet
After bursting onto the reusables scene with their planet-friendly, portable pottery adorned with eye-catching glazes, artist Clare Botfield and second-generation potter Renton Bishopric, of Pottery For The Planet, are harnessing the power of the sun to continue the fight to save the climate.
We caught up with Renton for our bumper 50th issue to learn more about the purpose and passion behind the gorgeous ceramics – head to the bottom of the article for an exclusive discount code!
What inspired the start of Pottery For The Planet?
As climate activists working on a range of campaigns together, we were both becoming increasingly disturbed by the amount of single-use coffee cups cluttering up landfill. Clare recognised that people are more likely to choose a reusable option if it was beautiful as well as functional, and had been inspired to make pottery travel cups for a number of years. There was some hesitation from me, due to the commercial nature of the idea. But in 2015, I finally saw the light and, together with fellow potter Stephen Roberts, produced the first run of Pottery For The Planet travel cups. This coincided with ABC running its first War on Waste series that focused on single-use coffee cups, and demand took off from there.
What have been your favourite moments along the way?
Seeing the reusable revolution take off after ABC’s War on Waste series aired, specifically the uptake of reusables by people who had previously not practised conscious consumption. Like many people, who would previously have considered themselves living an eco-conscious lifestyle, for us the War on Waste highlighted just how much more could be done as an individual towards reducing one’s footprint in terms of consumption. Together, we initiated immediate changes in our daily habits because of this increased awareness.
What was the most challenging part of that increased demand?
We had to very quickly figure out logistics systems to handle the increased demand. Originally, it was just me, Clare and Stephen making the cups, setting up market stalls, then later taking the orders and sending them out. Suddenly, we had to teach ourselves how to build a website, figure out efficient dispatch systems and hire team members to help us pack up all the orders. We also gained a lot of interest from stores and cafes wanting to stock our product, so needed to build a wholesale model into the business at the same time. Luckily, Clare is incredibly organised and great at figuring out systems, so she wrote all our standard operating procedures and taught herself how to code a website from scratch!
As a second-generation potter, when did you know that you wanted to make pottery your career?
After returning from a few years living and travelling overseas, I returned to my parents’ studio in Central Queensland and saw their lifestyle through fresh eyes. At this point, I jumped on a wheel and have been creating pottery ever since. Over the last two decades, this journey has seen many shifts and changes within the industry. It’s been a real highlight to be able to take my love of pottery and combine it with my love of the environment.
Tell us about your journey to becoming solar-powered…
Ensuring that our business’ energy demand is supplied by renewable sources has been a transition that’s been underway for a number of years. It began with committing to 100% renewable power through available retail suppliers and recently the installation of rooftop solar infrastructure large enough to supply power to run our large electric kilns. Although we’ve still got a way to go along our carbon neutral journey, it’s extremely gratifying to now open a kiln and know that all of the pieces in there have been fired by the sun.
Have you noticed differences with using the new electric kilns?
Incorporating electric kilns into our new studio process has opened up a completely new era for my work as a potter. We’re discovering all sorts of new possibilities for colour development through the highly controlled temperature and atmosphere inside the kiln. The finished results of some of our existing glazes that are coming out of the new electric kilns are blowing our minds! We can’t wait to have some time to start refining new recipes to add to our glaze range. We’ll continue to run both electric and gas kilns in our studio as they each offer unique results that, in some cases, the other cannot achieve. This ensures our range of glazes and colours remains diverse and interesting.
On a personal front, being able to program the firing cycle to start without my presence is amazing – instead of having to be at work in the dark to light a gas kiln, I can go for a surf on my way to work. That’s progress!
What do you want people to know about using solar?
Our recent project with The Climate Council is aimed at raising awareness in the wider community of the fact that solar technology has now reached levels of efficiency capable of powering industrial applications and processes, such as firing commercial kilns. This technology continues to improve, and who knows what will be possible in another five to 10 years!
How did COVID affect your business?
When COVID hit, we decided to create our own silver lining. 2020 and the COVID-related upheavals affected our business and, more importantly, the use of reusables immensely. We worked hard to introduce the tableware range I had been developing so that people could have beautiful ceramics while they were spending so much time at home. Our wholesale business was hit the hardest as we watched the heartbreaking shutdown of so many of our cafe and store partners. We’ve been so inspired to see the way these businesses pivoted and bounced back during their toughest times.
I had been wanting to get back into creating after years of focusing on the business side of things (which was necessary during our quick growth spurt), so I took the time to bring that vision for a new tableware range to life. With sales slower, we could take more time to create. It showed us how quickly we can pivot and I think brought us closer to our customers as well, as they played a part in telling us the types of new products they wanted to see. Our mug collection was born because so many of our customers and social media followers told us they were at home now instead of getting takeaway coffees and would love a mug in their favourite glazes! It’s saddened us to see many people forced to slip back into old habits of convenience, such as single-use coffee cups, due to the restrictions imposed. Encouraging people to get back to their reusable commitments is something all of our team is now working on daily.
Your glaze colours are so unique and eye catching, how do you create them?
As an artist you need to find an ‘edge’ to raise the level of your work. The glazing and firing process is one area that we do this. Glaze development is something that has been going on for thousands of years, starting out with simple two- or three-ingredient glaze recipes developed in China around the 14th century. Since then, glaze recipes have continually evolved with the discovery of new minerals and colourants such as oxides.
More recently, companies have created synthetic materials suitable for use in glazes and this has opened up a whole new realm of possibilities in terms of the colours you can create.
Many pottery supply companies offer pre-mixed glazes, which is essentially like buying paint. It’s extremely limiting for a potter and offers very little opportunity for creating a distinctly unique product, so we mix all of our glazes from scratch using raw materials sourced from all over the world.
Interestingly, we’ve had pottery supply companies tell us that they regularly have potters come in asking if they sell the glazes that Pottery For The Planet uses!
Where do you draw inspiration for your glazes?
We experiment a lot! When we designed the initial range, we considered the range of colours we wanted to include and played around until we found the right mix. There are some glazes that tend to change and evolve over time depending on firings – if there’s an improvement, we note what changed in the firing or the glaze recipe and we try to replicate it.
This means essentially relaunching the glaze and changing all the pictures on our website. A new glaze design can be in development for a couple of years before we launch the final version. We keep a collection of all our original glazes here at the studio and it’s so interesting to look at how each glaze has evolved over the years.
One of our earlier glazes, Outback, was inspired by an old glaze combination of my dad’s (Steve Bishopric), a flashback to Australia in the 1970s. Our Coral Dreaming glaze was created by our potter in the Margaret River region – Matt Griffiths – and inspired by the stunning colours of Australia’s Coral Coast.
We experiment in the studio constantly, exploring new forms and ideas in the production phase and then new glaze colours in the firing processes. One of my pottery mentors once told me, “You should have an experiment in every firing.” Although this is a lot of work, I do try to hold myself to this as I have come to realise it’s the way in which a potter can evolve their practice quickly. It’s very easy in life to get stuck in the familiarity of your comfort zone.
Why do you love what you do?
Both Clare and I, and everyone in our team, are driven by a combination of having fun making things that people love and doing something that’s great for the environment.
We’re absolutely committed to doing our bit to try and change single-use culture. To be able to do this through practising our art is something we’re stoked to have been able to achieve.
What have been the biggest challenges of Pottery For The Planet?
As our business has grown, logistics, and the related carbon footprint of moving products around, have proven challenging. We’ve worked creatively to do our best to keep our carbon footprint to a minimum with initiatives such as recently opening our West Australian studio and warehouse in Dunsborough. This will allow us to avoid shipping across the country to our wholesale and retail customers and significantly decrease our carbon emissions.
One of these challenges would have been Clare’s recent cancer diagnosis. How has this affected you and the business?
Clare’s recent health journey further highlighted the importance of living one’s truth. We had both been so focused on our business as it grew, that we had failed to maintain a work-life balance and had drifted away from many of our other passions. We’re now busy trying to reintegrate this balance into our daily lives.
What’s next for Pottery For The Planet?
Our team is always searching for the next pottery item that could help people along their sustainability journey. As a medium, pottery is the ultimate material with which to create reusables and we have so many ideas we hope to bring to life in the future.